Top Notch Packaging Machine Repair Service to Optimize Production Effectiveness
Comprehending the Key Parts and Repair Approaches for Product Packaging Device Upkeep
Efficient maintenance of product packaging makers rests on an extensive understanding of their crucial elements, including the frame, drive system, and securing devices. Recognizing usual upkeep issues, combined with the application of preventative techniques and fixing methods, can dramatically improve maker integrity. Furthermore, the choice of repair work methods, consisting of the use of OEM components and the importance of qualified technicians, plays a critical duty in decreasing downtime. To genuinely realize the details of these systems and their maintenance, one need to take into consideration the wider ramifications of ignoring these essential practices.
Secret Parts of Product Packaging Equipments
Packaging makers contain a number of crucial components that collaborate to make certain efficient and efficient product packaging procedures. At the core of these machines is the framework, which supplies architectural stability and houses the different operating components. The drive system, commonly a combination of equipments and motors, assists in the motion of elements, enabling exact operation throughout the product packaging cycle.
An additional necessary part is the conveyor system, which transfers items with different phases of the packaging process. This is frequently matched by sensors and controls that keep an eye on the setting and speed of products, making certain synchronization and reducing errors. The loading system is important for precisely dispensing the appropriate amount of item into packages, whether in liquid, powder, or strong form.
Securing mechanisms, including warm sealers or adhesive applicators, play a vital function in protecting plans, stopping contamination and prolonging rack life. In addition, identifying systems are essential for supplying needed product information, making sure conformity with guidelines. The control panel, equipped with user-friendly interfaces, allows operators to take care of maker functions, display performance, and make adjustments as required, making certain optimum performance and effectiveness in packaging procedures.
Typical Maintenance Concerns
Effective operation of product packaging machines relies greatly on normal maintenance to prevent usual problems that can interrupt manufacturing. Among these concerns, mechanical deterioration is common, especially in components like conveyors, motors, and seals, which can bring about unexpected downtimes. In addition, misalignment of components can cause inefficient procedure, triggering items to be improperly packaged or harmed during the process.
Another common upkeep concern includes the accumulation of dirt and particles, which can hinder the device's sensors and moving parts. packaging machine repair service. This not only affects performance but can additionally pose safety and security threats. Lubrication failures can lead to increased rubbing, resulting in getting too hot and eventual component failing.
Electric issues, commonly coming from loose connections or damaged electrical wiring, can interrupt machinery features, causing considerable production hold-ups. Software application glitches due to obsolete programs or incorrect configurations can impede the machine's procedure, necessitating prompt intervention. Resolving these typical maintenance problems proactively is crucial for ensuring optimum performance and durability of packaging equipment.
Preventative Upkeep Methods
Implementing preventative upkeep strategies is vital for sustaining the effectiveness and reliability of packaging equipments. These techniques next incorporate a systematic technique to maintenance, focusing on the normal examination and maintenance of equipment to preempt prospective failings. By sticking to an arranged upkeep program, operators can determine damage on components before they cause considerable failures.
Crucial element of a preventative upkeep strategy include routine assessments, component, cleaning, and lubrication substitutes based upon producer recommendations. Using checklists can improve this process, making sure that no important jobs are overlooked. Additionally, keeping exact documents of upkeep tasks help in tracking the equipment's efficiency over time, facilitating informed decision-making concerning future maintenance requirements.
Training staff on the significance of preventative her latest blog maintenance enhances conformity and promotes a culture of positive care. Executing a predictive maintenance part, making use of information analytics and sensing unit innovation, can additionally enhance machinery performance by predicting failings prior to they occur.
Repairing Strategies
When faced with malfunctions or inadequacies in product packaging devices, using systematic troubleshooting techniques is necessary for identifying and fixing problems swiftly. The primary step in efficient troubleshooting is to develop a clear understanding of the device's operational parameters and performance metrics. This includes assessing the maker's specifications, as well as any mistake signals or codes shown.
Next, operators should conduct an aesthetic assessment, checking for evident indications of wear, damages, or imbalance. This frequently consists of taking a look at sensing units, belts, and gears to determine prospective reasons for malfunction. Gathering functional information, such as production rates and downtime logs, can likewise supply insights into reoccuring issues.
When possible troubles are identified, making use of a rational strategy to separate the origin is essential. This might need testing specific elements or systems in a controlled manner. Participating in conversations with operators who connect with the machinery on a regular basis can generate useful feedback regarding uncommon actions or patterns.
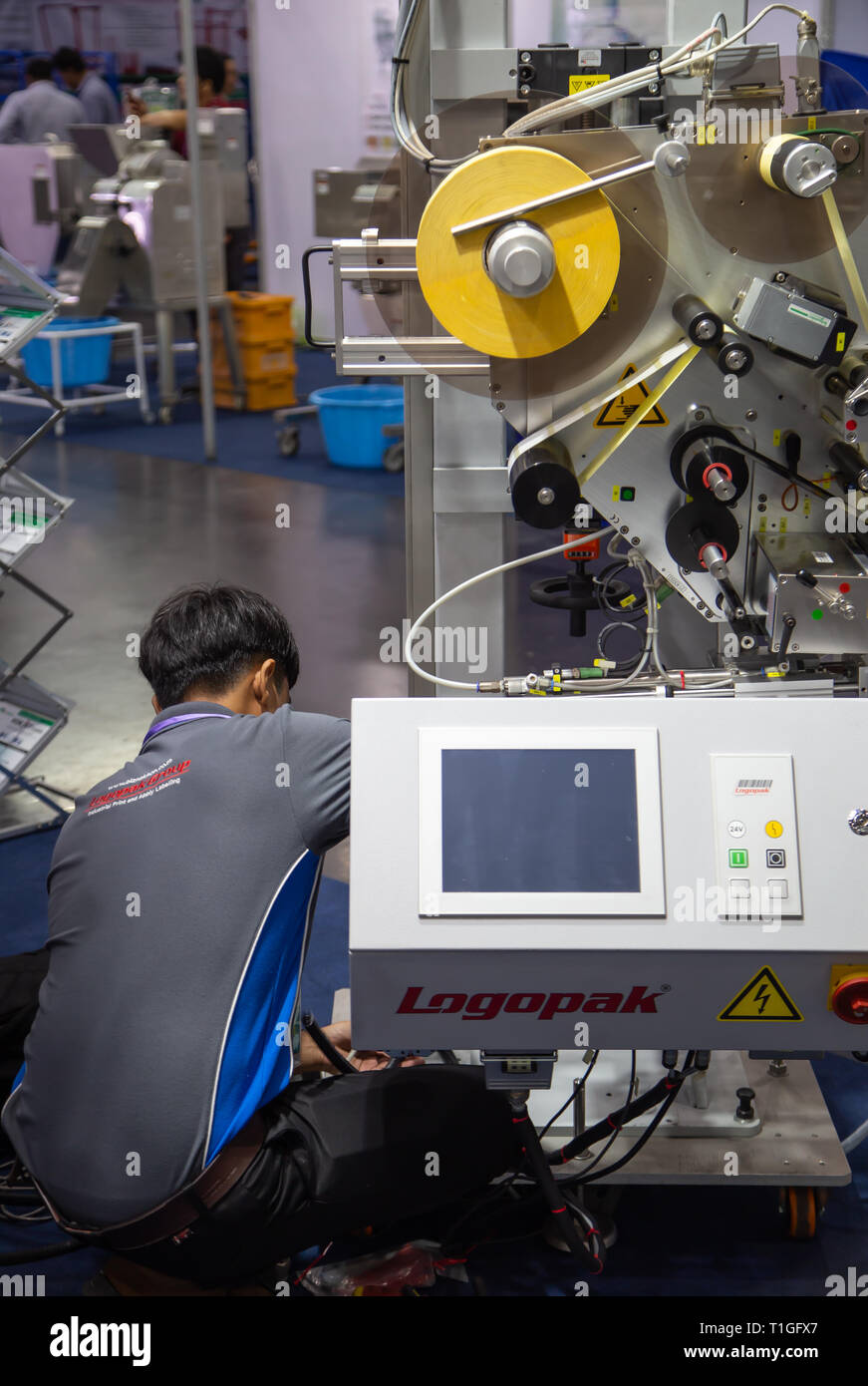
Fixing and Substitute Ideal Practices
A comprehensive understanding of repair service and replacement best methods is vital for keeping the longevity and efficiency of product packaging devices. Routinely examining the problem of machine elements permits for timely intervention, preventing more substantial issues that can bring about pricey downtimes.
When fixings are necessary, it is crucial to utilize OEM (Original Tools Supplier) parts to this hyperlink make certain compatibility and performance. This not just maintains the honesty of the maker but additionally supports guarantee contracts. Furthermore, it is suggested to maintain an inventory of critical spare parts to help with quick substitutes and lessen functional disturbances.
For complicated repair services, engaging licensed technicians with specialized training in packaging machinery is advised. They have the experience to identify concerns properly and execute repair work effectively. Recording all fixing activities and components replacements is vital for preserving a thorough maintenance history, which can aid in future troubleshooting.
Finally, implementing a positive method, including routine inspections and anticipating upkeep strategies, enhances the dependability of product packaging devices. By adhering to these finest methods, companies can ensure optimal equipment efficiency, decrease operational risks, and prolong tools life-span.
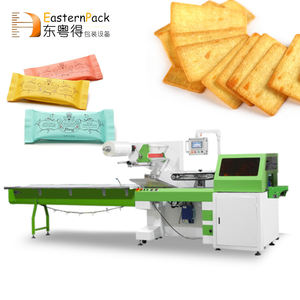
Conclusion
In verdict, a comprehensive understanding of product packaging machine components and reliable maintenance strategies is essential for optimum efficiency. By carrying out these practices, organizations can make sure the longevity and effectiveness of product packaging equipments, inevitably adding to improved operational productivity and decreased expenses (packaging machine repair service).
Efficient maintenance of packaging devices pivots on an extensive understanding of their crucial elements, consisting of the framework, drive system, and sealing systems.Efficient operation of packaging machines relies heavily on normal upkeep to protect against usual problems that can interrupt production.Carrying out preventative upkeep methods is important for sustaining the effectiveness and reliability of packaging devices. Furthermore, preserving accurate documents of upkeep tasks aids in tracking the device's performance over time, assisting in notified decision-making relating to future upkeep needs.
